Plant Construction Management

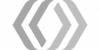
We provide you professional resources to operate and manage integrated Spool Management System (SMS)
Which includes as a minimum, control of documents & drawings, control of data pertaining to material receipt and material control, Pipe Spool Fabrication Monitoring and Control, Weld Database Management, NDT Tracking, Flange Management. Support Management, Spool Tracking, Spool Erection Tracking, Spool Painting and Tracking, Invoice Details and final documents at fabrication shops location.
A dedicated team shall be mobilized to accomplish the total scope of work with proper coordination and interface with Contractor, Spool Fabricators and other agencies involved in the project execution.
What We offer in this service
Spool Operation & Management
- Developing the Project frame for Spool drawing processing.
- Selection of Field Weld/Shop weld / Field Fit weld location on the spool isometric drawing based on the project information provided by Contractor
- Generation of Spooled isometric drawings and individual Spool piece drawings from MATC files of isometric extracted from PDMS models. Also generate erection isometrics showing the spool numbers and erection MTO.
- Revision change control and maintaining consistency in joint numbers. This may require verification of old revision with latest revision.
- Back check of the Spool drawings by comparing with Contractor’s original drawing to ensure the integrity of attribute data, text information etc.
- Auto-Extraction of Weld data, Spool wise BOM, NDE, PWHT, PMI, CRA root visual, Painting, Insulation etc. and Pipe Support details for both at shop and field.
- Weld identification of primary pipe support and structural supports
- Specification break shall be considered as spool limit
- We number all the pipe spools and provide final documentation with all changes marked on hard copy & electronic copy of spool drawings and isometric drawings.
Piping Database Management
- Document/Drawing and Revision Control
- Fabrication & Erection Material Simulation, tracking, monitoring, Controlling and reporting.
- Work Order Planning and Fabrication Control
- Welding and Inspection Control (Both Fabrication & Erection)
- Spool Movement Control
- Field Piping Erection, test pack, Punch clearance and system/subsystem clearance Control
- NDT requirement tracking and generation of outstanding report
- Pipe Supports Fabrication & Installation Management
- Management information system for project progress.
- Personal Computer (PC) tracking, allocation, issue and reconciliation
- Maintain & ESD details in the system
- Tracking of painting & internal /external coating on the applicable spools
- Forecasting of front availability based on material arrival dates.
- Line continuity studies & reporting of site work front generated with respective adjoining spools.
Material Traceability
This is very essential documentation required for the project. A system of recording Test certificate numbers (TC numbers) (unique number to be assigned) and heat numbers to be made available in the system. Against each part number used in shop and field the heat numbers with TC numbers will be recorded and a link shall be created for easy access to the scanned copy of TCs.
Job Card Preparation
We ensured that all spool sheets/erection isometrics released for construction have to be carrying the same information available on Contractor’s Engineering isometrics.
PARASCADD has prepared the job card based on material availability and issued isometrics
- Prepare material issue tickets for job cards.
- Issue job card and drawings to the fabricator at the fabrication shop
Weld/NDE Data Management
- Database installation at fabrication and erection location
- Issue job card and drawings to the fabricator.
- Daily entry of all reports into SMS as advised by Contractor
- QC clearance reports weld history sheet to shop/site
- Test Pack Cell: We set up the group of technically competent personnel’s, to prepare the test packs, based on the P&ID markups. The isometrics are to be grouped based on the markups, attach necessary formats in the packs, create a database for the packs and upload the same to SMS.
- Drawings attributes may be given in database format and spool/erection drawings that are generated will need to incorporate this data from the database given by Contractor
- We includes the details required for shop fabrication and site erection (such as painting specification, NDE, Hydro testing etc.)
Piping Workload
Completion Schedule Requirements
PARASCADD will perform following.
- Ensuring that all Pipe spool drawings meet the requirements of all standards, etc.
- Furnishing progress reports (Daily, weekly and monthly).
- Generate the details on productivity of shops, productivity per fitter/welder, weld statistics etc.
- Performing / coordinating all engineering related queries, as required by the requisition, and its referenced publications, and/or drawings.
Work Schedule
PARASCADD submit the detailed mobilization plan, work schedule (for the entire scope of work).The manpower deployment should be self-sufficient and competent to address the absenteeism of any employee arising out of R&R or any other reasons.
We prepare and make available daily shop production and overall spool status on line to review all aspects of progress. We submit progress reports in such forms as maybe agreed between parties during project set up in software. These progress reports include,
- Forecast completion for key events
- Daily/Weekly status report at shop/field
- Progress relative to the original programs.
- Raw material status report
- Spool wise outstanding material list
- ISO wise material constraint list
- Areas of concern.
- Any other reports as desired by the Contractor based on software.
Quality Assurance & Quality Control
PARASCADD submit a check lists for each activity, prior to start of work, for review by Contractor. We ensures their deliverables are free from error or omissions by internal checks and verifications.
Procedures
- Revision handling
- Work flow from material receipt to spool dispatch
- Work order issue with pick list to shop floor
- Material/weld traceability recording system
- Welder tracking/performance procedure
- Punch list recording systems
- Punch list category data base /updating
- Recording spool erection progress/status
- Report generation procedure i.e. type of reports, fields, publishing periods etc.
- Spool joint marking procedure
Documentation
The following documents shall be submitted as a minimum on completion of the work;
- History of all QA/QC reports/records/procedures from material inspection to dispatch
- Line history sheets dully signed by all concerned
- History of all material management information
- As Built Pipe Spool Drawings/erection ISOs (marked with any authorized changes made during the execution) hard copy and electronic copy.
- Approved deviation requests (If applicable)
- An electronic single data base of all information (weld management, NDT, material traceability, spool details, test pack information etc.) to be submitted. This must have facility to search, filter and produce reports.
Key Performance Indicators (KPI)
The Following KPIs are also met and monitored by PARASCADD:
- Stop work notice should reach fabrication shop within two working days of instruction received from Contractor
- For all revision ISO drawings received from Contractor’s Engineering team, PARASCADD prepares an impact report within two working days
- After each simulation, job card should be issued and reached its destination within two working days.
- To ensure real time progress report, PARASCADD input all data on the day itself. PARASCADD ensures that reports are generated based on real time data.
Safety Regulation
PARASCADD executes all the scope of work strictly in accordance with the Safety Rules for employees and Visitors with proper personal Protective Equipment as applicable.
The following is the brief checklist of the points to be taken care of during execution of the order:
- Engineering Accuracy
- Dimensional tolerances /correctness
- Accuracy of data transfer to spool sheets
- Verify the spool marks with CONTRACTOR isometrics
- Material inventory, storage & issue control
- Materials/welding traceability tracking and documentation
- Consistency in joint numbers
- Revision handling
- Priority wise spool sheet generation and material allocation
- List of known flaws and root causes (To be provided by CONTRACTOR at later date)
- SUBCONTRATOR based on their experience shall also add points to the above SUBCONTRATOR’s checklist shall have adequate hold points to cover above points.
Quality & Safety
PARASCADD’s QA/QC Plan Service Agreement is always executed in accordance with Company Quality assurance and control, Inspection approved by the Contractor/Company. PARASCADD maintains strict adherence to Contract Permit to Work System, Safety Rules and Regulations, QA/QC requirements as specified in the mandatory Service Agreement during the execution of these works.
This includes qualifying all personnel of PARASCADD’s construction supervision team as per:
- Contract requirements,
- Company Quality Assurance and Control,
- Inspection requirements as per Project QA/QC Execution Plan in Company documents.